Offset Printing Rubber Ink Roller
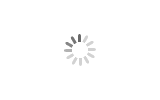
- Ceres
- Guangdong ,China
- 5-15 working days
- 5000pcs per onr month
In the printing process of the ink roller, it is necessary to ensure the good working stability of the inking system, the uniformity of the ink and the continuous ink supply. The ink roller should have good ink affinity, elasticity, and solvent resistance. Therefore, the ink roller is generally composed of a metal roller core and a rubber layer. The core should have good rigidity and strength, and have the ability to resist deformation.
We provide ink roller for Heidelberg, KBA, Roland, KOMORI, Akiyama, Shinohara and other offset printing machines. We also provide customization function. Customers who want to customize need to provide AI or PDF files
Offset Printing Rubber Ink Roller
Introduction:
Ink roller is composed of rubber layer and metal core roller. Rubber is the main part of ink roller, it plays the role of uniform transmission of ink. Metal roller core is the framework of printing ink roller.
Types:
Printing roller;
Stretch roller;
Back-up roller;
Hot stamping pressure roller;
Water roller;
Traction roller;
Ink roller;
Gravure pressure roller;
Routine maintenance
1.The rubber roller must be cleaned carefully and cleanly after get off work every day or after each batch of products is printed. Avoid oxidation of the surface layer of the rubber roller and the pigment and resin in the ink to form a smooth and hard film, which affects the transfer of the ink.
2.Prevent debris and ink shovel from scratching and crushing the ink roller. During the printing operation, the offset press table should be kept clean and tidy. Do not pinch debris and ink shovel into the ink roller.
Recomand products:
Cylinder Jacket
Wash Up blade
Dampening sleeve
Gripper Bar
Our Services